
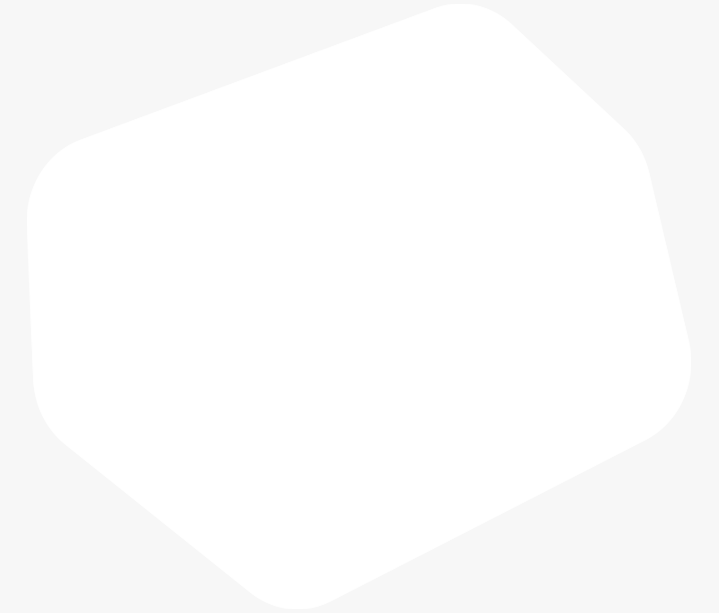
The real need for speed
Exclusive car manufacturer Koenigsegg uses High Performance Computing to speed up development
A top speed of 440 km/h sure sounds impressive but for Swedish super sports car manufacturer Koenigsegg, a reduction of overall development cost by 1,5% has a sweet ring to it, too. The cost reduction was made possible through using advanced Cloud Technology for a highly complex Computational Fluid Dynamics simulation. Going for a cloud-based service, Koenigsegg was able to reduce setup cost, streamline the simulation process, and arrive at the desired result faster than usual. That’s just the right way of doing things for a super sports car that can easily outrun a starting jet airliner.
Car enthusiasts will be familiar with the name Koenigsegg. The Swedish manufacturer of super sports cars was established in 1994 and is considered a leading designer and manufacturer of high-performance sports cars. With engines producing up to 1000 kW, Koenigsegg cars can outrun pretty much everything on earth with wheels and wings. It is easy to see that the development of such an extremely performant car needs to take all aspects of the vehicle into consideration. Brakes must withstand the enormous forces when reducing acceleration and momentum and the chassis has to be aerodynamically optimized, too. A car that is moving at a third of the speed of sound needs all the traction it can get. Any element of the cars body has to fulfil its task in perfecting downforce and at the same time posing minimum resistance to the surrounding air.
The choice: Wind tunnel or simulation
In order to develop such elements of the cars body, Koenigsegg needs to understand how air flows over its cars. Technically, there are two ways of doing this: The first and traditional way is to put the physical body into a wind tunnel, the second way is to simulate the flow of air in a computer using a technique called Computational Fluid Dynamics (CFD). Both methods have pros and cons, so companies in the automobile industry use both techniques alternately. Computational simulations are often used throughout the whole design phase. Wind tunnel tests usually come into play only at certain phases of the design, since they are considered to be much more expensive from a cost and time point of view.
Especially in the development of high-performance cars, intensive CFD simulations are carried out in order to reduce the cost of wind tunnel testing. Due to the high accuracy needed to replicate a cars every geometric detail, such models can be very large and complex. Rotating wheels and integrated components such as heat exchangers, fans and condensers all add to the overall model structure. In simulating such large models, the use of High Performance Computing (HPC) can make a significant difference. Past experience has shown that the full aerodynamic design of a megacar or hypercar can be almost entirely conducted using CFD with minimal road and wind tunnel testing. However, in a production environment tight deadlines must be met, placing an emphasis on the use of significant HPC resources.
Megacar development posed new challenges
Koenigsegg was looking for CFD-simulation models when developing their first megacar, the One:1. Named megacar because of its engine, which can deliver an output of more than one megawatt of power, it was clear from the beginning that this car would require the best aerodynamics possible. Koenigsegg wanted to perform simulations of the air flow over the car which were sufficiently detailed to model real physical effects accurately. Such simulations require suitable simulation software and expensive computer resources, which are normally beyond the means of an SME, even a highly specialized and successful company as Koenigsegg. However, the use of Cloud-based HPC offers the possibility of running such simulations on a pay-per-use basis, which is financially viable for an SME. The challenge was therefore to demonstrate the feasibility of using cloud-based HPC resources, the porting of a suitable simulation code to such resources and the cost-effective outcomes of the simulations.
Complex simulations such as CFD-models must be run on High Performance Computers (HPC). These consist of clusters of processors that can work in parallel and are connected by high-throughput links. Dividing complex calculations between processor cores in an efficient way is a gargantuan task in itself, a HPC cluster is at least as much dependent on its hardware as on its controlling software. On top of this scheduling and controlling software sits the actual CFD-simulation software. All these components are managed by highly trained and specialized staff, usually a mix of employees of the HPC-provider, the CFD-software manufacturer, and the client whose simulation model is being processed. As a result, CFD with HPC-systems is expensive. It has been expensive in a dimension that has had smaller companies like typical SMEs shy away from the necessary capital investments and pass HPC solutions altogether. Even an established high-tech business like Koenigsegg was expecting a huge up-front capital investment. But since 2013, a new initiative has been making waves in the HPC-scene. Fortissimo is a project funded by the European Commission in order to strengthen the global competitiveness of small and medium enterprises (SMEs) in Europe. As a means to do this, Fortissimo uses a cloud-infrastructure to provide SMEs from different vertical markets including automotive with easy access to computationally intensive digital simulations.
High-performance computing and CFD moves into the cloud
The CFD market can be characterized as having customers with two distinctly different drivers: On the one side heavy CFD users with high budgets, which are typically Original Equipment Manufacturers (OEMs) who are moving into more complex physics with improved accuracy and associated business impact. The followers, on the other end of the spectrum, have modest CFD resources available. Typically, these are small to medium enterprises (SME) who employ engineers with limited skills in CFD and use commercial software with licenses limited for budget reasons. These limits usually entail a maximum number of concurrent sessions or parallel threads, which severely hamper the software when it comes to more complex tasks. They are therefore often obliged to “dumb-down” the level of simulation refinement they may achieve or need for real breakthroughs. In any case, both customer groups share a latent need for access to scalable, cost-effective CFD.
As hardware costs have plummeted over the past ten years, the real cost of CFD simulations should have come down significantly. However, although it is cheaper than ever to procure multiple CPU systems, the license cost for CFD have not decreased in a similar manner. Thus, as a HPC-company adds extra CPUs to its computer resources, the software vendors have priced their solvers on a per parallel thread, or groups of parallel threads, basis. This has resulted in a high proportion of companies having to severely restrict the type or size of the computer simulations that they undertake.
The equations underpinning a CFD analysis have to be solved by the computer in an iterative manner and require thus very powerful and costly computer infrastructures and very long processing times which usually called for traditional parallel or cluster computing. However, HPC Cloud-based CFD simulation has become a possible alternative to large clusters. By moving simulations of CFD models on a cloud based HPC environment, processing times can be impressively shortened. Moreover, the anticipated royalties and utilization costs of such services can be drastically reduced, enabling the simulation code provider to reach new markets, while SMEs that were unable to “purchase” such services can be given the opportunity to do so, moving from stand-alone and effort/resources consuming applications to more flexible SaaS solutions.
Team of experts collaborated efficiently
Cloud-enabled technologies not only increase the cost effectiveness but accelerate the uptake and application of more complex CFD, which in many cases is required to capture the science necessary to influence product development. Through utilizing a cloud infrastructure as a base, opportunities for optimizations can be identified and used along the entire value chain. This approach offers a broad spectrum of possibilities, beginning with more precise design of complex workpieces through the use of computer-supported visualization; continuing via reducing the time-to-market thanks to simulated tests on prototype models; and finishing with saving material costs through the virtual manufacture of prototypes to fine-tune production. In the case of Koenigsegg, the company approached NTUA, a research organization with expertise on interoperability, system integration design and decision support systems. The specialists from NTUA had extensive experience with ICON, a provider of CFD simulation software. Through Fortissimo, they were able to use HPC resources provided by CINECA, a leading HPC center.
The experiment started from the design need of Koenigsegg, building a CFD/CAE process workflow, based upon ICON FOAMpro CFD software, to be integrated with the Fortissimo infrastructure, so as to give end-users a seamless access to Cloud HPC resources for their CFD-based problem solving activity. Before becoming a Fortissimo user, Koenigsegg had only limited computer resources available in-house and little or no experience in HPC-based CFD. Through the cloud-based HPC solution, Koenigsegg was able to conduct 100% of the aerodynamic development of the Koenigsegg One:1. In less than eight months, hundreds of simulations to test various configurations have been carried out. Very accurate, however very computer intensive, transient detached eddy simulation solvers for drag and lift prediction of supercars were employed, enabling Koenigsegg to avoid wind tunnel testing altogether. The results were an impressive 250% increase in down-force with only a 15% increase in drag at 250km/h and with a 50% higher down-force at 440km/h, the vehicle’s maximum speed.
Impact and Business Benefits
The provision of a Cloud-based HPC solution can bring significant innovation into the marketplace. In particular, the innovation would be derived from the ability to assemble significantly cheaper compute farms for CFD analysis than ever before, combined with open source solvers. In addition, ICON has already demonstrated the maturity of automatic design optimization technologies. If those are combined with open-source CFD solver technology, industrially supported by ICON, they can offer significant price point advantage over existing manual CFD simulation methods. For Koenigsegg, the benefits obtainable by the use of the Fortissimo HPC-Cloud can be quantified as a 5% saving in operational costs, a 30% saving in design costs, a reduction of 50% in wind tunnel and physical testing, a 60% saving in prototyping costs, and a 30% shortening of the time to market. Furthermore, savings in development were about €90K per year on the design process, corresponding to a 1.5% reduction in overall development costs. These calculations take into account a computing cost on the Cloud-based HPC system of around €100K. Summarized in more general terms, the project has shown, that the use of HPC-based simulation, supported by external software and expertise, led to a return of investment in less than three months for the production of a new car configuration. Significant costs could be saved and transferred to other critical parts of the development and production process.
The Fortissimo initiative has gained valuable insight through the Koenigsegg One:1 project, too. It demonstrated, that the Fortissimo infrastructure was an ideal base to port existing simulation code solutions over to HPC Cloud infrastructures. This way, end users could have instant access to a “one-stop-shop” which offers simulation services on demand, while users were able to obtain the results of their simulations in less time, and with a pre-defined cost per simulation.
Share it:
